Boliden Kevitsa trusts DBS' GearWatch condition management system to increase the life and health of their gear systems
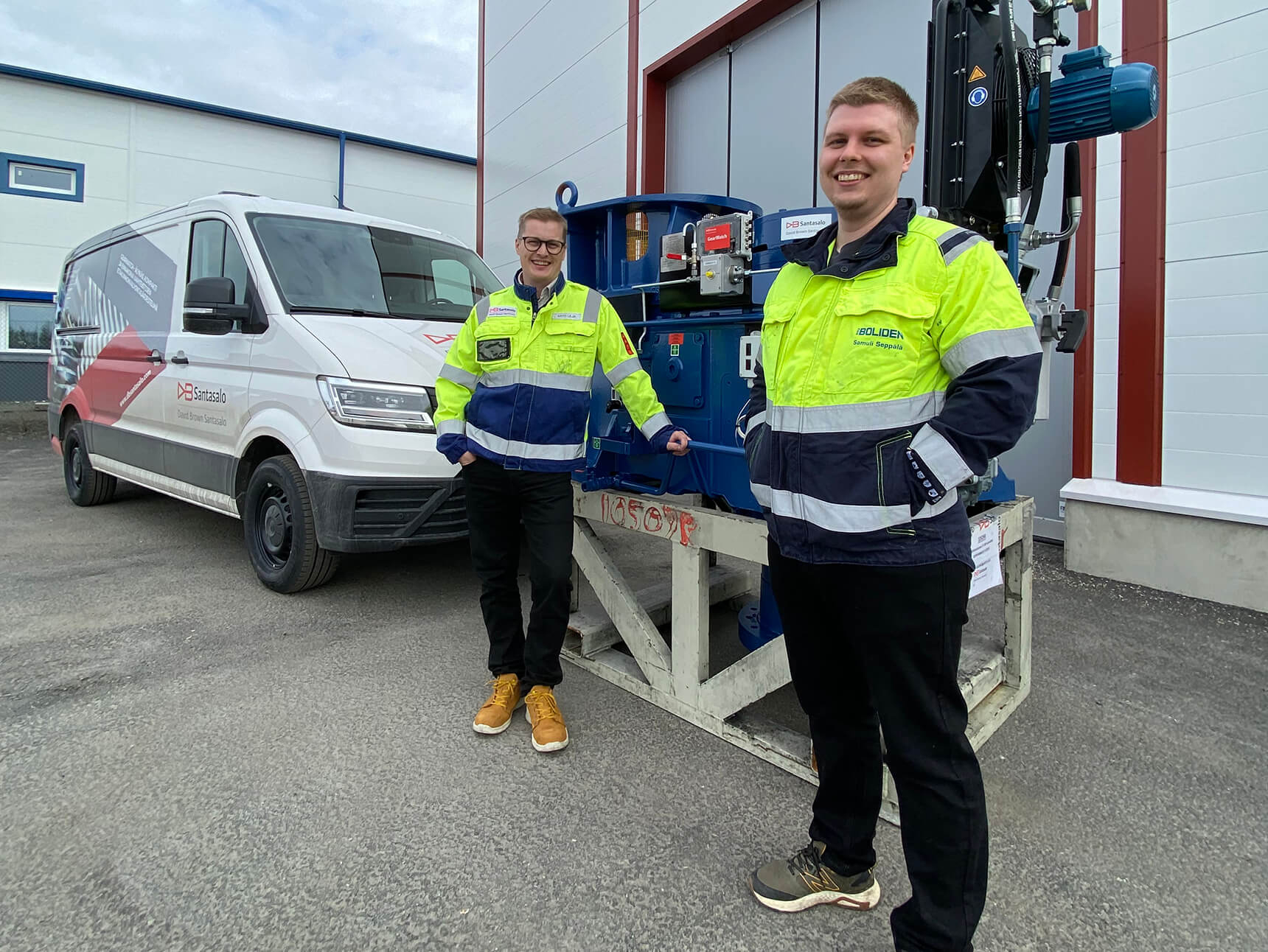
The GearWatch condition management system from David Brown Santasalo (DBSantasalo) helps to detect changes in the condition of industrial gears at an early stage, so that gearbox failures can be prevented in many cases. DBSantasalo’s customers have received clear benefits from using GearWatch, as their customer Bolidens Kevitsa has experienced.
“GearWatch is a system developed for monitoring the condition of gears, the goal of which is to detect deviations and faults as early as possible, when the condition of the gear can be influenced. In the best case, this can prevent the actual failure of the gear.” DBSantasalo Product Manager, Mika Hirvonen says.
GearWatch can measure several parameters related to the operation of different industrial gearboxes. The measurements include particle counting and oil quality monitoring, and in addition to these, vibrations, temperatures, oil pressure and rotation speed.
Monitoring the lubrication oil particles
Through GearWatch, DBSantasalo specialise in the monitoring of the lubrication of oil particles, because the functionality of the lubrication is a very important factor for the operation and long life of the gear.
“Different sensing packages are available, e.g. Oil Analysing Unit. All sensors in use are connected to a Smart Terminal, from which the data is sent to the GearWatch cloud service. In the cloud service, the data can be read by the customer and DBSantasalo's condition monitoring centre, so the customer also gets analytical support from professionals specialised in the condition monitoring of gears.” Hirvonen mentions.
It is also possible to integrate GearWatch into the customer's condition monitoring system. At its widest, the integration can even be taken so far that the alarms become automatic work orders for the customer's maintenance system.
Boliden Kevitsa trusts the GearWatch condition management system
Boliden Kevitsa's condition monitoring expert Samuli Seppälä talks about his experiences using GearWatch and the beneficial aspects he noticed.
“We already have several GearWatch condition monitoring systems in use, the first of which was already installed in 2019. During the last year we have started to significantly increase the number of systems we have in place, in connection with the second update project. This set includes 14 gears, to which GearWatch systems were also added when the lubrication cycle was updated.
Seppälä mentions that there have been positive user experiences with GearWatch. Boliden Kevitsa has had more than 20 units of equipment using the same technology in the past, and many good experiences have been gained from them over the years.
“With the help of the new condition monitoring technology, dozens of different malfunctions have been caught and the necessary repairs have been scheduled for the planned maintenance shutdowns. This has resulted in significant savings for us.” Seppälä continued.
It is possible to safely increase the lubricant change interval
When measuring the purity class of the oil, DBSantasalo also add measuring the water content of the oil to GearWatch's wear particle calculation. The condition of the lubricant and the functionality of the filtration can also be monitored based on that. In light of this information, the lubricant can be kept as efficient and long-lasting as possible. At the same time the chemical condition of the lubricant is regularly monitored with laboratory samples, meaning it is possible to move from periodic oil changes to need-based oil changes.
“In our biggest lubrication cycles, we have moved away from periodic oil changes, so the oils are changed based on condition. In some locations, it has been possible to drive for up to five years with the same oils, when previously the oils were changed annually. It has not only saved costs, but also the environment, because there has been no need to change the oil that is in working condition”, Seppälä mentions.
GearWatch helps reduce the carbon footprint of maintenance
A longer oil change interval results in savings in euros, but at the same time the environmental burden is reduced, as oil with good characteristics is not changed unnecessarily. The same also applies to the prevention of failures. When deviations in the object's condition are detected as early as possible, timely remedial measures can often stop or limit the progression of the failure, which means that the need for spare parts is significantly reduced. This reduces costs and saves the environment.
GearWatch produces continuous trend information
The sensors of the GearWatch system measure continuously and the data is transferred to the user interface, where the trend information can be immediately analysed. Automatic alarm limits have been set for all trends, from which alarms are sent if necessary. The data produced by GearWatch is in an easy-to-analyse format in the user interface. For example, particle counting is based on the idea that practically no metallic wear particles should come off from a new and in good condition gear. Thanks to constant online information, it is easy to conclude that the situation is good. Then, when metal particles start entering the lubrication circuit, it is known that the wear process has started. In practice, the only sources of metal particles are gear bearings, gears or the housing.
“At DBSantasalo, we have a long history of using this technology and a huge number of monitored objects, so based on our experience, we know how to support the customer in analysing the results and determining possible corrective measures,” says Mika Hirvonen.
Easy installation
GearWatch installations can be done on completely new gear systems, as well as serviced gears. In Kevitsa, some GearWatch installations have been made in connection with maintenance or modernisation. Installing the system usually only requires a few hours of downtime, during which the oil hose connections are made. Planned downtime is always utilised in the installations.
“Our customers are able install the GearWatch equipment themselves, as installing the devices is relatively easy, but we are always on-hand and involved when required. GearWatch systems can be installed in all manufacturers' gears, regardless of the make or model". DBSantasalo's Sales Director, Harri Koivuvirta says.
GearWatch also works in rolling stock
“GearWatch can also be installed to monitor the rolling stock of the open pit,when the system is implemented in connection with the next maintenance”, DBSantasalo’s Northern Finland Unit Manager, Arto Lilja says.
Boliden Kevitsa's Samuli Seppälä sees the condition control situation as regards Boliden Kevitsa's refinery as good. He considers GearWatch to be a very easy way to also include the critical components of mobile equipment in the scope of condition monitoring.
“With regard to mobile equipment, we use online vibration measurements, which naturally have their own challenges in mobile devices. I would see that condition monitoring via lubricant is an easier way to perform condition monitoring, especially for rolling stock”, Seppälä concludes.