Condition monitoring solutions for the future
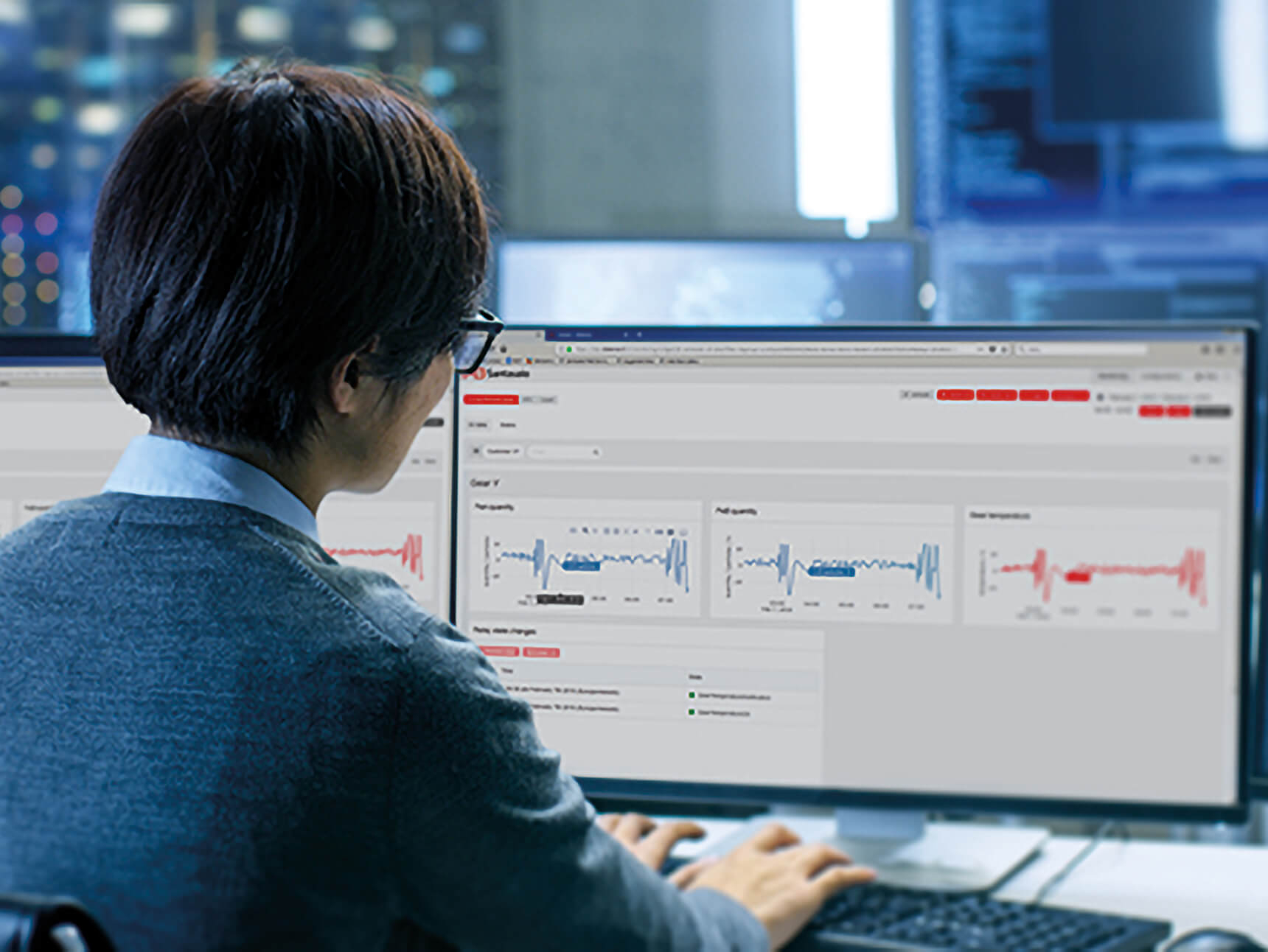
The modern age has brought digitalisation to old processes, saving time, money and resources through automation. We are constantly evolving to learn how we can do things easier, slicker and better than we have before.
As an end user, we expect more and more from our digital lives. Whether it’s how much of our lives we can fit into our mobile devices, how hard our laptops can perform for the remote worker or how fast our internet connections will run. We demand perfection and continually look for the next innovation to enhance our lives.
At David Brown Santasalo, we have embraced digitalisation to enhance our design, engineering and manufacturing processes. In an industry where we constantly create, innovation is key. Our gearboxes operate in harsh environments from extreme heat to freezing temperatures, where failure is not an option. We find synergies between highly skilled operatives and how their methods can be enhanced with the introduction of state of the art machinery.
Take our new 3.5m gear diameter Klinelnberg machine, which uses state of the art technology to check the profile, lead and pitch of some of the largest high quality gears in the world, following machining. The only machine of its type in the UK, it can also be used as a Coordinate Measuring Machine, and to do some basic NDT checks, which means we can check fabrications, gear cases and gears all on the same machine. Checks are completed to ensure that the gear teeth have been machined correctly and that the gearbox meets strict design criteria. This, alongside our stringent test processes ensures that David Brown Santasalo gearboxes are robust and reliable.
But, what happens after the gearbox has left the production line and is in its natural habitat? How do we ensure the gearbox is performing to the high specification it was designed to and how do we continue to deliver added value in a tangible way? The answer in part, is condition monitoring. A way to remotely monitor the health of a gearbox whilst it is in operation. With this method we can spot issues before they become a problem helping you to avoid minor repairs and prevent gearbox failure.
The next generation of condition monitoring
David Brown Santasalo is taking gearbox condition monitoring into the next generation of its development. Developed by a team of specialists with a deep understanding of drive system technology and rich heritage of designing and manufacturing gear units.
This state of the art solution introduces a new phase in condition monitoring. Unlike main stream solutions currently in the market, oil particle counting is the main condition monitoring method, which brings a completely fresh approach to prolonging the life of gear units.
Particle counting gives a warning of the failure at a much earlier stage than gearbox vibration can, especially on low speed applications. By adding oil particle counting into the mix, along with 24/7 remote monitoring and cloud based technology, it adds a new dimension that will support customers’ process reliability. Imagine, proactive maintenance that detects defects at such an early stage using sensor technology.
Having the ability to monitor the health of the oil in the gearbox, means potential gear unit failures can be detected months, or even a year in advance. This enables the user to plan maintenance activities around operational requirements. An exciting concept when we consider the timescales and costs involved in building a new gearbox and, should shutdown occur, the detrimental effect this could have on a company’s production capabilities, which can lead to a huge impact on revenue.
Why oil particle counting & quality measurements?
The operation and longevity of a gearbox requires the lubrication and related monitoring and maintenance operations to be carried out correctly. The main function of lubrication is to provide a metal contact preventive oil film on the rolling surfaces of bearings and gear wheels. In addition, it transfers the heat generated by the bearings and the gears to the environment and removes impurities and wear particles. In addition, the oil film between the tooth flanks is essential for the operation of the gear unit.
Small metal particles in the lubrication oil are the first indicators of initial damage. Online monitoring and trending of the metal particle’s quantity and size, enables the early detection of damage in gear teeth or roller bearings.
Typically, hundreds of litres of oil circulate through a gearbox. The GearWatch oil particle counter is placed on the pump-filter-unit of the gear, whilst an inductive sensor detects oil circulation from both ferromagnetic and non-ferromagnetic particles. The particle counter is also immune to air bubbles and other dust present in the oil, ensuring it provides an accurate reading.
The next step in lubrication condition monitoring is through an oil quality sensor, which enables online monitoring of the gear unit’s lubrication oil condition. The user is kept informed of changes in fluid condition, as it occurs and can react to unpermitted operating conditions. Analysis can then be made about the condition of the oil, for example ageing or mixing with other fluids.
Why we must embrace digitalisation
On a general level, the infrastructure for digitalisation has been significantly improved, while today it’s considered “normal” to be able to handle large amounts of data and use it remotely. When we begin to understand the capabilities and opportunities of these developments; suppliers, manufacturers and customers can all benefit.
GearWatch provides the end user with peace of mind, it delivers a ‘one shop service’ meaning we monitor, analyse the findings and propose a course of action to rectify the issues. Then if needed provide the repair or maintenance to get the machine up and running. Available in three packages; DBS GearWatch Standard, DBS GearWatch Oil Monitoring and DBS GearWatch Pro, meaning it is fully adaptable to the customer’s requirements.
The future of condition monitoring is bright, and certainly for the GearWatch model, there is much more to come. The next phase will be launched in Autumn of 2018 and will offer a tailored monitoring system for gear units & drive trains within selected parameters. David Brown Santasalo will continue to innovate, to ensure we stay ahead of the curve.
To find out more about GearWatch, please click here.